

HART: HART stands for Highway Addressable Remote Transducer.DNP3 has another variant named secure DNP3, which takes care of secure authentication and other security features at the application level and is always recommended instead of DNP3. Efforts have also been made to provide safe authentication at the application level. At the data link layer, it has the ability to detect any errors in data transmission by means of CRC check. It operates at the application, data link and transport layers thus, it is a three-layer protocol.ĭNP3 design focused more on maximizing system availability and less on confidentiality and integrity. It was developed in 1993 and is widely used in the USA and Canada. DNP3: DNP3 stands for Distributed Network Protocol.
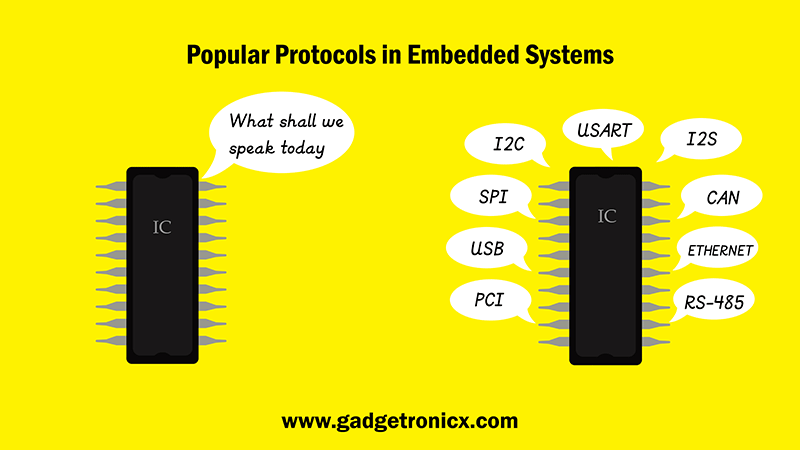
Modbus has several security concerns – lack of authentication, lack of encryption, lack of message checksum and lack of broadcast suppression. Master/slave is a communication model in which one device (master) controls other devices (slaves). In a typical Modbus network, there are 247 slaves and one master.
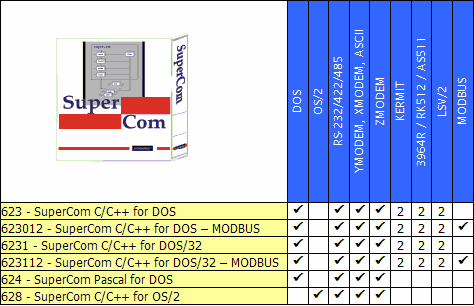
Modbus is a request-response protocol and operates at the application layer of the OSI model. Modbus communicates raw messages without authentication or any overhead. It is open-source and freely distributed and can be built by anyone into their equipment.
List of serial communication protocol full#
RS-232 supports full duplex transmission method and allows only one transmitter and one receiver to communicate at a time. Due to low cost, simple design and enough space for multiple receivers, varieties of connectors are available to connect to its interface. RS-232 is primarily used for low speed over short-distance requirements.
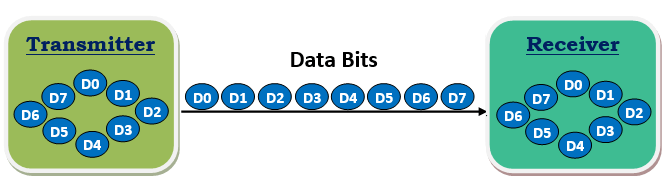
In a typical ICS system, the following protocols are widely used: RS-232 and RS-485, Modbus, DNP3, HART, TASE 2.0 and ICCP, CIP, PROFIBUS and PROFINET, FOUNDATION Fieldbus, BACnet and more. These protocols were first designed for serial connection but, with time, have evolved to support and run on TCP/IP protocols over Ethernet networks. All the systems, interfaces and instruments in an ICS system use different protocols for real-time communication and data transfer. Communication protocols used in ICS systemsĪs described above, due to ICS being different from IT systems in many aspects, traditional IT protocols cannot be used in ICS systems. Thus, IT and ICS systems are altogether different and pose their own challenges in terms of maintenance, security and operations. On the other hand, ICS systems focus more on detecting, monitoring and controlling physical equipment and processes using sensors, actuators, controllers, PLC ( Programmable Logic Controllers ), PCD (Process Control Dynamics), BAS (Building Automation System) and more.
List of serial communication protocol software#
IT systems basically focuses on the development, maintenance and use of computer systems, software and networks for the processing and sharing of data. Note: The terms “ ICS” and “SCADA” are used interchangeably in media. Programmable Automation Controllers (PAC).Industrial Automation and Control Systems (IACS).Supervisory Control and Data Acquisition ( SCADA ).Components of ICSĪ typical ICS system is made up of the following components: Thus, ICS systems ensure industrial operations run smoothly and give the operator an easy way to monitor, control and manage industrial processes remotely. If it is, then it may send commands to the machinery to shut down. For example, ICS systems may get data from remote sensors to check whether a particular piece of machinery is overheating.
